All the parts your products will need for production all the way through December 2021 should be covered by purchase orders now.
That’s the advice DiMonte Group is hearing from key semiconductor companies that we rely on in our design work. They have urged us to contact all our clients to encourage them to work proactively with their suppliers, starting right away.
The Covid pandemic has caused major disruptions to industrial supply chains, and the ripple effects for industry might last even longer the virus itself. This applies to a wide variety of materials and finished components, and is especially true for electronics.
This of course is not the usual procurement model. Typically we buy small quantities of parts for development, prototypes, and pilot production through authorized distributors. Then when the unit volume numbers run into the hundreds or thousands, you (or your contract manufacturer) place blanket orders for production, with scheduled releases. This allows the distributors to aggregate demand and place volume orders with the semiconductor companies, and in return they can offer you better volume pricing. A significant portion of the stock carried by the large industrial electronics distributors—like Arrow, Avnet, and Future—is allocated inventory, being held to service these blanket orders. Since most of the volume demand is known in advance and allocated, your effective lead time for production parts is only a week or two.
Unanticipated demand—volume orders that are not covered by these allocations, and that exceed the general inventory carried by distributors to cover prototypes and pilot runs—will quickly run into the lead-time to make new parts from scratch. The factory lead-time for a new run of semiconductor parts can be 26 weeks or longer.
In the first quarter of 2021 there have been many news stories about automotive factory shut-downs caused by a shortage of the electronic chips that go into cars—engine and transmission controls, body controls, and infotainment. Because of the pandemic, around the end of the first quarter of 2020, automotive factories had basically shut down. The chip manufacturers were fortunately able to shift some of their production to the increased demand for consumer electronics and personal communications devices that families were buying to survive the quarantine at home.
Late in 2020, the automotive industry started to revive—more suddenly than anticipated. When the car manufacturers started placing orders on the semiconductor companies, they found—to their surprise—that what they needed right away was not available any time soon.
As calendar 2021 progresses, the semiconductor manufacturers are trying to catch up. But there is very little unallocated inventory in the supply chain—neither factory stock, nor inventory at the distributors—and lead-times have been moving out farther and farther. There are already shortages today on many key components utilized not just in cars, but in many industrial applications as well:
- Microcontrollers
- Accelerometers
- Linear integrated circuits
- Power MOSFETs
- Monolithic ceramic capacitors
Here is a chart showing how lead-times have recently increased, based on data from key suppliers:
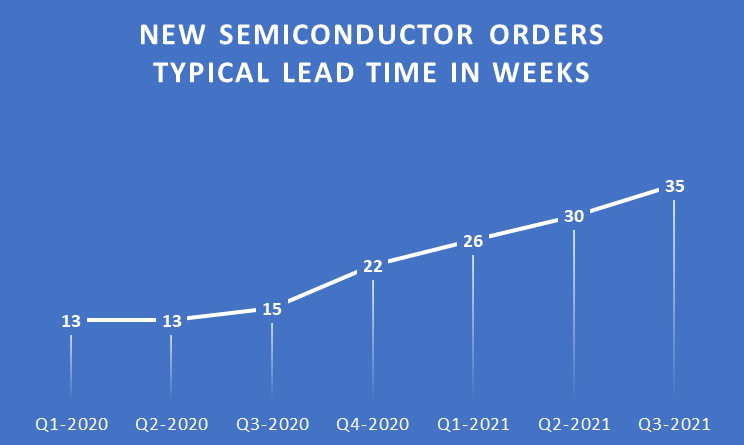
If you would like to check this out further for yourself, here are some links:
- An article on chip shortages, dated 2/21/21, by IHS Markit: https://ihsmarkit.com/research-analysis/semiconductor-component-supply-chain-shortages.html
- A lead-time index for electronic parts other than semiconductors, provided by Avnet, one of the largest industrial electronics distributors: https://www.avnet.com/wps/portal/abacus/resources/content-library/lead-time-guide/
Trying to protect future builds, some companies—especially contract manufacturers—have been placing large blanket orders for parts they MAY need, trying to get allocations on the books without firm forward commitments to actually take delivery on the parts later in 2021. In reaction, major semiconductor manufacturers are notifying purchasers that they must agree that all purchase orders, new and old, must be formally accepted in writing as NCNR, non-cancelable, non-returnable, or will be canceled. This is a defense against oscillating order/cancel cycles that could make it impossible to know what the real demand might be.
As of this writing (mid-March, 2021), the factories have for the most part already allocated all their production for Q2 2021 (April-June) and are already well underway selling out Q3 2021 (July-September). If we assume that the general economy will continue to rebound from the pandemic, Q4 supplies will soon be allocated as well.
As a design engineering firm, DiMonte Group does not typically have to be overly concerned about our clients’ production plans once we have helped them develop working systems. But in today’s supply chain climate, we need to alert you that the usual order of things does not apply. You need to start ordering parts that you will need for production six or more months from now—in many cases even before your designs are fully complete, tested, and certified!
When we convey this message to our clients, we sometimes hear that they are relying on the “purchasing power” of their large contract manufacturer. That misses the point. For the coming months, if needed parts are not already known and accounted for in the supply chain, they simply will not exist, and nobody will be able to get them, whether they are a small start-up, or General Motors.
For the last few months, we have been working with our clients and representatives of key semiconductor manufacturers to develop procurement plans for future production.
Please keep these issues in mind as you plan your development and production activities for 2021.